Faber
Services
The company Faber is the plastic machined parts and modular conveyors specialist. However, the services we offer are not limited solely to modular solution
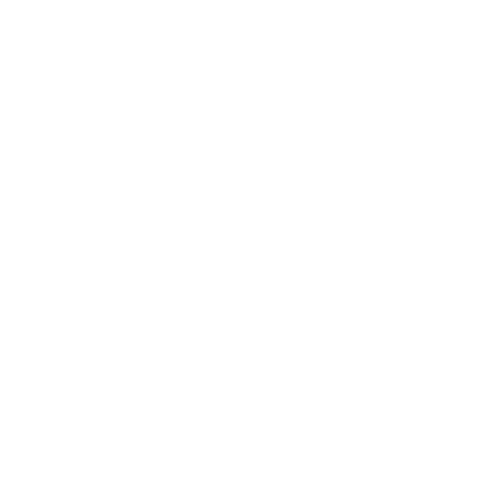
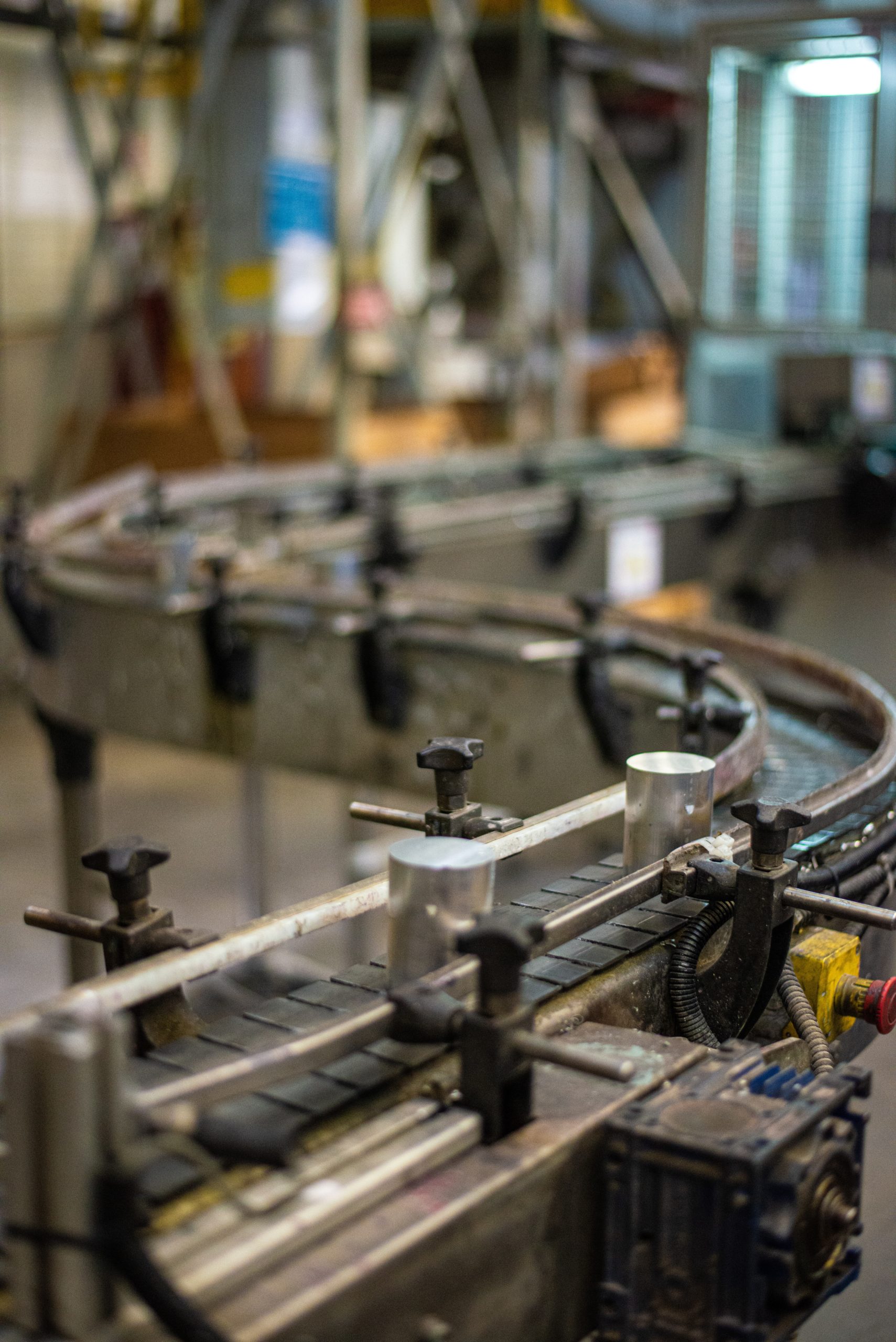
We support you in your projects with a range of services:
- Customisation and support: A Faber expert will visit your site to help you define your needs and guide you through the investment process. By talking on site, you will be able to identify the solutions best suited to the configuration of your workshops and the specific features of your business. You will receive a complete study.
Feasibility study and production: based on your
specifications, we work together to develop a technical solution, often
illustrated by drawings, photos or videos of similar projects.
Scanning and measuring: On request, we can scan your bottles and machine frames in your workshops, to reconstruct their geometry.
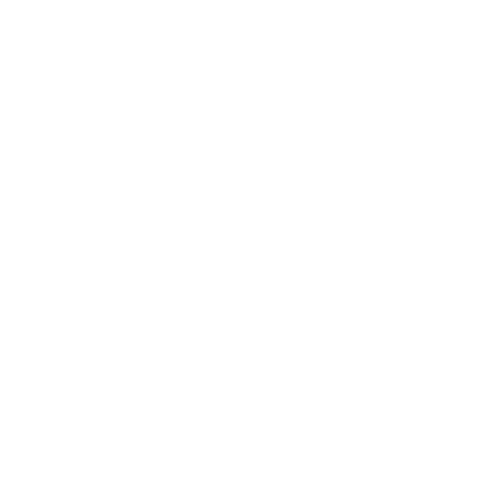
- Installation and commissioning: We can install and start up your equipment on your packaging machines, wherever you are located. Our technicians will come to your premises to install your equipment. No need to mobilise your staff, we take care of everything, from design to installation.
- Assembly: Our team will help you assemble and adjust your new equipment.
- After-sales service: Faber puts people skills first. Our advisers have acquired technical know-how to support and advise you, but the main objective is to bring your project to a successful conclusion by finding the most suitable solution. Don’t hesitate to contact us on + 33 (0)3 24 27 79 83, at export-faber@hellomoov.com or via our online contact form.
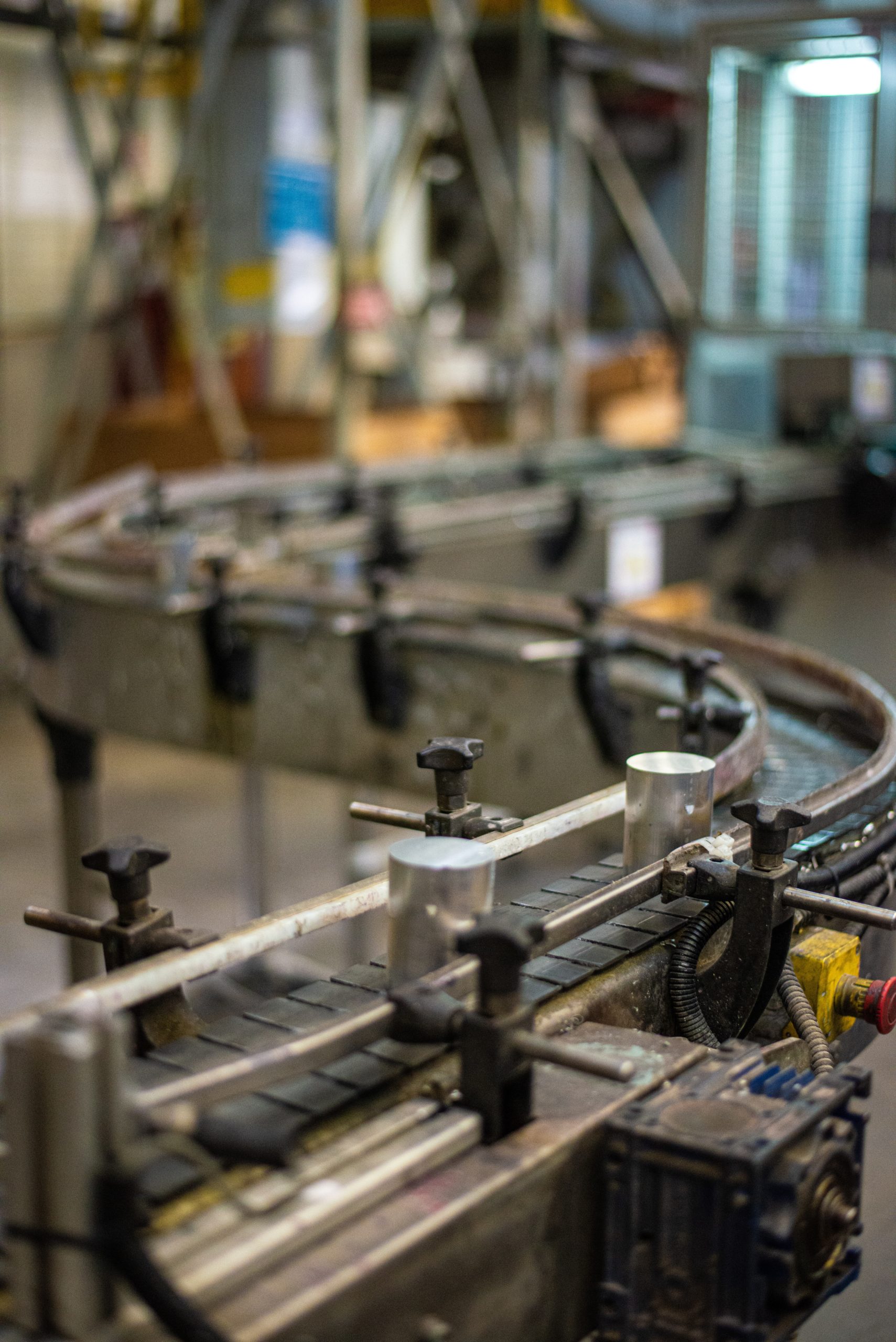
Maintenance contracts
FABER offers several maintenance contracts for the solutions installed in your workshops. 3 different levels are available, depending on your needs.
The contract “Assistance” covers part of the 1st level maintenance and supports the subscriber’s maintenance department through regular recurring visits by specialist technicians. This will enable us to advise or prevent any production downtime.
-Level 1 annual maintenance visit, without parts.
The “Preventive” contract means that level 2 and 3 preventive maintenances can be entirely carried out by the manufacturer. The contract covers labour, travel and all moving mechanical wear parts. Intervention times, the number of visits per year and the frequency of component replacement are defined according to the type and size of the subscriber’s line, as well as the original operating conditions.
– Level 1 annual maintenance visit, without parts.
– Level 2 preventive maintenance, including parts
The aim of the contract “Full” is to wholly subcontract curative and preventive maintenance to the manufacturer. The contract covers travel, labour, electrical parts (sensors, motors) and moving mechanical wear parts. Intervention times, the number of visits per year, and the frequency of component replacement are defined according to the type and size of the subscriber’s line, as well as the original operating conditions.
– On-site technical training
– Level 1 annual maintenance visit, without parts.
– Level 2 preventive maintenance, including parts
– Associated spare parts
A question?
Feel free to call on us to make you a quotation or to arrange for an expert assistance to help you achieve your projects